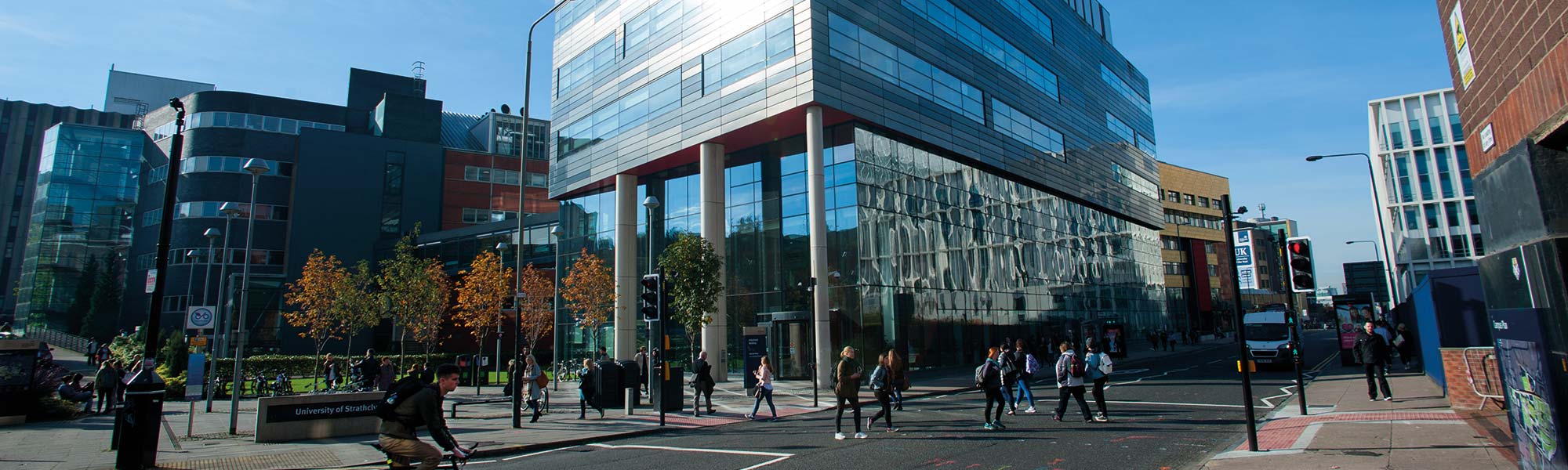
Dr Aleksey Reshetov
Research Associate
Digital Factory
Back to staff profile
Publications
- The ESAFORM benchmark 2023 : interlaboratory comparison benchmark for the characterization of microstructural grain growth and dynamic recrystallization kinetics of a single-phase Ni-base superalloy
- Agirre Julen, Bernal Daniel, Flipon Baptiste, Bernacki Marc, Brüggemann Holger, Bailly David, Merklein Marion, Hagenah Hinnerk, Risse Jan Henning, Madej Łukasz, Muszka Krzysztof, Cichocki Kamil, Poloczek Łukasz, Bylya Olga, Reshetov Aleksey, De Micheli Pascal, Barlier Julien, Stark Andreas, Suhuddin Uceu F H, Staron Peter, Klusemann Benjamin, Galdos Lander
- International Journal of Material Forming Vol 18 (2025)
- https://doi.org/10.1007/s12289-025-01893-9
- Benchmarking mean-field models available in commercial FE software in application to two-blow forging of IN718 alloy
- Reshetov Aleksey, Bylya Olga
- Material Forming - The 26th International ESAFORM Conference on Material Forming – ESAFORM 2023 26th International ESAFORM Conference on Material Forming, ESAFORM 2023 Materials Research Proceedings Vol 28, pp. 683-692 (2023)
- https://doi.org/10.21741/9781644902479-74
- Aspects of high strain rate industrial forging of Inconel 718
- Reshetov A, Stefani N, Bylya O, Krishnamurthy B, Blackwell P
- Superalloys 2020 The Minerals, Metals & Materials Series, pp. 461 - 470 (2020)
- https://doi.org/10.1007/978-3-030-51834-9_45
- The influence of the microstructure morphology of two phase Ti-6Al-4V alloy on the mechanical properties of diffusion bonded joints
- Yakushina E, Reshetov A, Semenova I, Polyakova V, Rosochowski A, Valiev R
- Materials Science and Engineering: A Vol 726, pp. 251-258 (2018)
- https://doi.org/10.1016/j.msea.2018.04.052
- The occurrence of ideal plastic state in CP titanium processed by twist extrusion
- Reshetov Aleksey, Kulagin Roman, Korshunov Alexander, Beygelzimer Yan
- Advanced Engineering Materials (2017)
- https://doi.org/10.1002/adem.201700899
- Applicability of JMAK-type model for predicting microstructural evolution in nickel-based superalloys
- Bylja Olga, Reshetov Aleksey, Stefani Nicola, Rosochowska Malgorzata, Blackwell Paul
- (2017)
Back to staff profile
Projects
- CTA AI in Manufacturing Programme
- Reshetov, Aleksey (Principal Investigator) Sherlock, Andrew (Principal Investigator) Wilson, David (Fellow)
- The CTA programme seeks to target, identify, down select Canadian technology solutions providers specialising in Artificial Intelligence (AI) software and mentor those companies in how to market and deploy their software solutions within the UK manufacturing sector.
NMIS and appropriate sub-contractors will assist in this process ensuring that the chosen companies have appropriate maturity in their solutions and seek to provide engagements to manufacturing organisations across various sectors i.e. automative, aerospace, renewable energy and etc. - 31-Jan-2024 - 21-Jan-2025
- FutureForge strategic programme
- Perez, Marcos (Principal Investigator) Bylya, Olga (Fellow) Reshetov, Aleksey (Research Co-investigator) McDonach, Alaster (Fellow) Khatuntseva, Anastasia (Researcher) Andreu, Aurik (Fellow) Fleming, Christopher (Fellow) Chalkley, Eleanor (Fellow) Falsafi, Javad (Principal Investigator) Huang, Jianglin (Fellow) Rosochowska, Malgorzata (Fellow) Khismatullin, Timur (Researcher) Liang, Sha (Researcher) Millar, Richard (Researcher)
- Aiming to further develop fundamental understanding in key areas related to closed die, open die and isothermal forging, and exploring promising new capabilities, such as process instrumentation & data control and lubrication & coatings for hot forging at high temperatures
- 01-Jan-2019 - 31-Jan-2020
- FutureForge - Validation geometry
- Perez, Marcos (Principal Investigator) Bylya, Olga (Fellow) Easton, David (Fellow) Reshetov, Aleksey (Research Co-investigator) Ntovas, Michail (Researcher) Fabris, Mathieu (Researcher) Falsafi, Javad (Researcher) Huang, Jianglin (Fellow) Rosochowska, Malgorzata (Fellow) Chalkley, Eleanor (Fellow)
- Develop fundamental understanding in key areas related related to open, close-die and isothermal forging, exploring promising new capabilities, such as ultrasonic non-destructive characterisation and process instrumentation and data control.
- 21-Jan-2018 - 31-Jan-2019
- SAMULET Project 4 Task 4.3.1 and Task 4.3.2
- Rosochowski, Andrzej (Principal Investigator) Ewing, Helen (Co-investigator) Ion, William (Co-investigator) Qin, Yi (Co-investigator) Blackwell, Paul (Researcher) Gzyl, Michal (Researcher) Qarni, Muhammad Jawad (Researcher) Reshetov, Aleksey (Researcher) Wood, Paul (Researcher) Yakushina, Evgenia (Researcher)
- Several process options for the manufacture of components are beset with either quality or economic deficiencies. For example, the cleanliness of surfaces of aerospace components is critical to the production of sound welds using electron-beam welding technology; deficient cleaning methods would result in defective welds. Again, the conversion of Titanium alloys into aerospace components is currently attended to at temperatures at which tool-materials deteriorate rapidly, incurring a prohibitively high tool cost. Converting aerospace materials at high-temperatures would also require specialised tool-materials that are more expensive to cut and capital expenditure that is, typically, four times greater. Current practice is to shoehorn the controlling parameters to enable the manufacture of components. Continuation in this manner is unacceptable from an economic viewpoint. Considering that component designers need to be sufficiently conversant with the geometrical, functional and manufacturing constraints while evolving the form of the component, it follows that new processes, regardless of whether these relate to surface preparation (cleaning), processing at elevated temperatures or to machining to reduce further surface finishing requirements, may only be adopted efficiently, after the critical controlling parameters have been quantified. Project 4: Novel and Transformed Processes, attends to the quantification of the key controlling parameters. Research in the group of novel and transformed processes is with a view to acquiring the know-how to enable the design of components and the associated processes along the value-adding chain. This group refers to the laser cleaning of aerospace materials and components for subsequent processing, since it is known that several defects arise from the failure to meet quality standards. Two aspects of Project 4 refer to the high-temperature conversion of materials into aerospace components. The first of these refers to a new means of manufacturing components at low temperature by introducing a new form of raw material - this ultra-fine-grained variant enables the operation of the conventional processes (diffusion bonding and super-plastic forming) at significantly reduced temperatures, resulting in reduced manufacturing cost. This fine-grained variant will be manufactured and subjected to component forming exercises to demonstrate the new economic balance in manufacturing aerospace components. The second process is hot-die forging of aerospace components. The current practice of bashing Titanium alloys at very high temperatures into a rough form and then whittle away to arrive at the final form is recognised as being expensive. The need to bash the material arises from the fact that the work-material cools too rapidly to operate at the lower forging speeds that can be attended to in presses of lower capital expenditure. If one were to operate at lower temperatures, smaller presses may be used but this balance between bashing the metal at high temperatures and squeezing the work-material at lower temperatures has yet to be defined. The proposed research will define the parameters critical to operating at lower temperatures. The final project refers to an elegant approach to removing the excess materials remaining on components in a manner that reduces the amount of additional downstream processing of surfaces to meet performance standards. By quantifying the character of the cutting tool and the machine on which excess material is removed, the technology will enable the operation of the metal-removal system in a manner that recognises the fact that the character of both, the cutting tool and the machine-tool influence the cut surfaces. Each separate process will assume a role in more cost-effective conversion of raw materials for the aerospace industrial sector and would also impact on the nuclear and automotive industrial sectors.
- 01-Jan-2010 - 31-Jan-2014
Back to staff profile
Contact
Dr
Aleksey
Reshetov
Research Associate
Digital Factory
Email: aleksey.reshetov@strath.ac.uk
Tel: 534 5507